The Important role of “Owner” Stakeholders in the Problem Solving of Major Building System Failures
By Alex Kouri
Part 1 – “Drinking from the Fire Hose” The Flood at Kensington Tower and Subsequent Elevator Repairs
The Problem & Objective
In the Fall of 2022, on a Saturday evening at the Kensington Tower Apartments, a major failure occurred at a coupling on the main (6”) fire sprinkler line. Water gushed out at a rate of nearly 1000 gallons per minute, quickly filling the basement and elevator pits. The Kouri Management team responded within 30 minutes and got the main fire supply valve shut off from outside the building before the basement filled up and major systems were compromised. In addition to all of the damage associated with having 3 ft of water in the basement of a highrise building, the elevator pits were filled with water and both elevators were shut down. The elevator contactor arrived the next morning and immediately got to work cleaning and inspecting all of the elevator equipment. Within a few hours they had one of the elevators up and running but could not get the other elevator started. The elevator contractor continued to work for the next few days to no avail. They represented that we were out of options and the next step would be to work up a bid for replacing the elevators.
In the midst of an insurance claim, it can be tempting for contractors and principals to rely on claim payments to solve the major problems that have occurred. Finding or creating alternative solutions to replacing a major building system requires significant effort and diligence on the part of the Principals and often represents less profit for contractors. Alternative solutions must often be created under time pressure depending on the nature of the loss. The forces at play tend to nudge all parties in the direction of total loss if insurance is involved. In reality, insurance coverage very often falls short of expectations and repair solutions are needed to avoid significant capital infusion. Especially for larger historic properties or aging buildings with large mechanical systems, replacement value insurance is not always a financially feasible option.
In the case of the Kensington tower apartments, Kouri Management had the elevator contractor work up the bid for replacement but at the same time engaged the technicians who had inspected the elevator directly and also talked to other contractors in the industry. Kouri Management pushed back against the conclusions and additional inspections and tests were initiated. It was discovered that a large motor-generator was electrically shorted and was one of the many potential issues preventing the system from operating. Repairing the motor represented a significant expense estimated at $25,000 and in no way guaranteed that the system would run. At the same time the bid came back for replacement of the elevators at $900,000, the bid was processed by insurance and it was determined that only $350,000 would be covered by the policy. It would take 4-6 months to complete the elevator replacement. The building had difficulty functioning with a single elevator due to resident traffic and major ADA issues when the remaining elevator went down, this created significant time pressure on decision making. It was ultimately decided that the motor-generator repair would be made. Repair work was completed and the motor-generator was reinstalled. The system did not startup and significant troubleshooting time was incurred. Kouri Management oversaw the troubleshooting and determined that the technicians available lacked the experience with older equipment to effectively find the root cause of the problem. An older more experienced technician that Kouri Management had worked with in a different market was brought in to look at the situation. After a day of troubleshooting and testing the problem was isolated to a small circuit board that controlled the magnetic field of the elevator hoist motor. The board had been damaged somehow in the loss event and was not outputting the correct signals. The elevator contractor went out to its suppliers and determined that the circuit board was obsolete and could not be sourced for replacement. The elevator contractor again declared that the only option was full replacement of the system. Kouri Management immediately took measures to determine if the board could be reverse engineered and fabricated, additionally a thorough search of the internet and various aftermarket electronics suppliers was made. The effort yielded a number of options, the best being a small electronics repair/resell firm on the east coast. The firm had the exact circuit board in stock; it had been taken from a decommissioned system and had been refurbished. The circuit board cost less than $500. The board was purchased and the experienced technician was brought back in for installation. After a day of install and additional troubleshooting the elevator was up and running and has been running since. Most of the costs associated with the repair were covered by insurance.
Although it can take significant financial and administrative resources, finding the root cause of a building system’s problem and balancing the cost of fixing it against the capital expense of replacing the entire system is essential in mitigating the financial risks involved with operating large building systems. Finding the root cause to a complicated problem requires persistence and constitution on the part of the Principals and property manager. The experts and contractors serve their purposes but they can’t (and should not be allowed) play the role of “Owner”
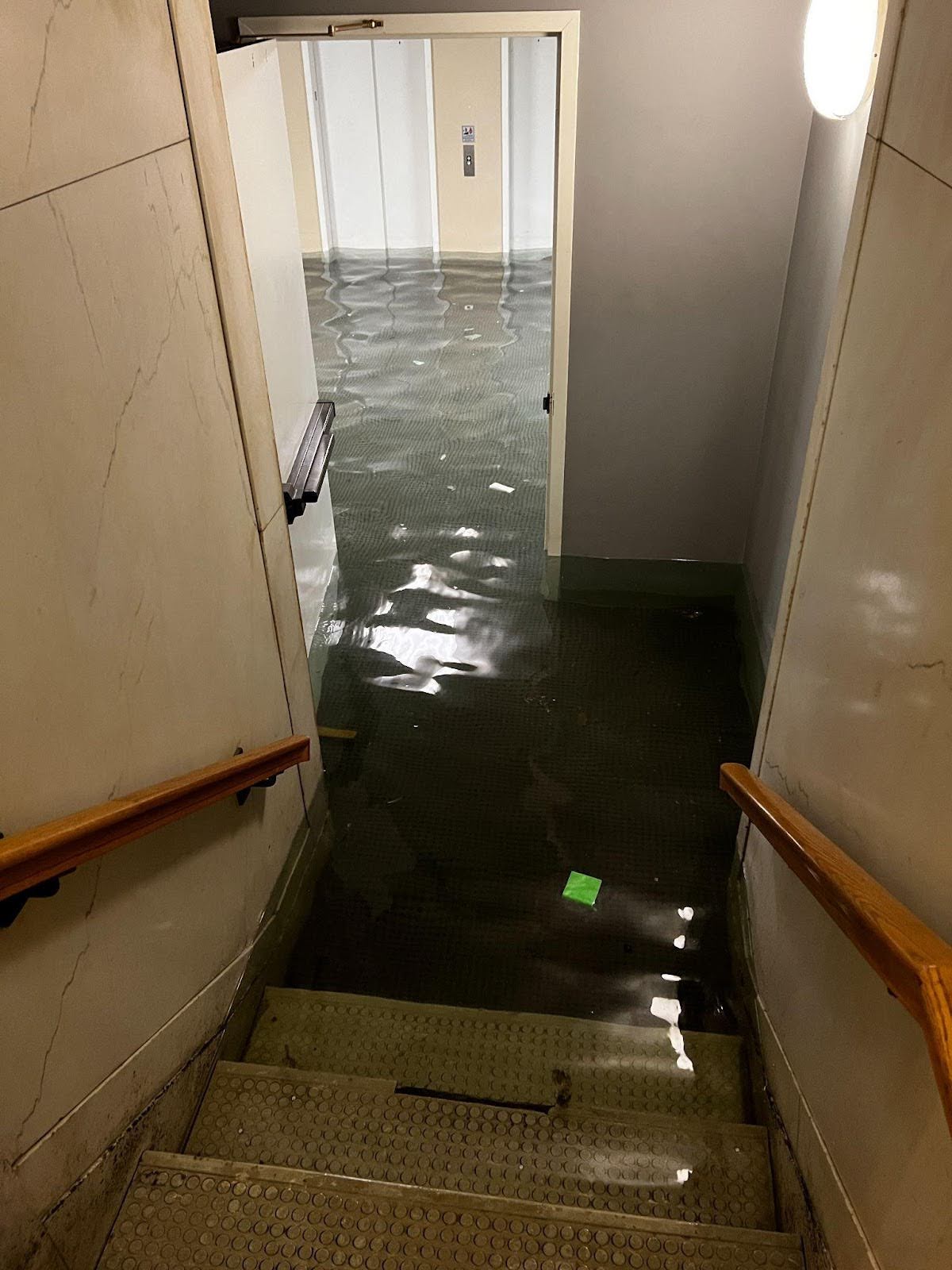
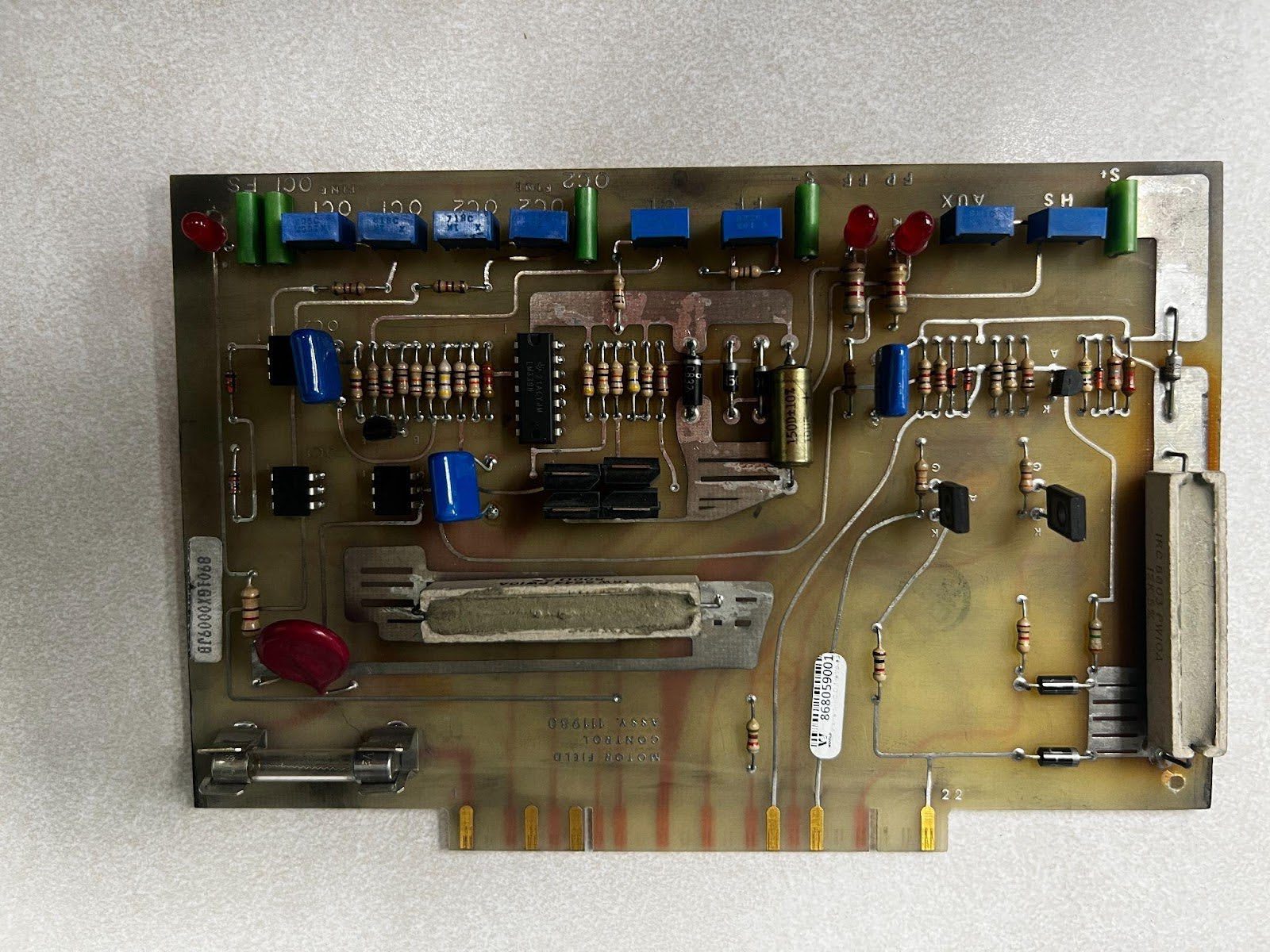
Part 2 – “Escrow Elevator Eval” Elevator Repairs during the purchase of the Fleming Building
In the 2nd half of 2022 KMC Properties LLC (a holding company owned by Kouri Management leadership) began negotiations to purchase The Fleming Building in downtown Des Moines. A purchase agreement was eventually signed at a very favorable price for KMC Properties LLC. This transaction was extremely important to KMC Properties LLC as it would complete its open 1031 Tax Deferred Exchange and prevent a significant tax expense for other recently sold properties. Kouri Management began conducting due diligence on the property and the documentation supplied by the seller. It was revealed that one of the 3 elevators (Elevator #2) had been shut down for over 2 years. The documentation indicated that Elevator #2 had failed the 5 year load test. A bid to replace the Sheave (The part of the hoist assembly that interfaces with the hoist cables) was included in the due diligence documentation received from the seller. The bid was for a cost of $60,000, a significant number but also small enough to raise questions as to why the seller had waited 2 years without taking action.
The documentation and repair bid for Elevator #2 was submitted to 3 different elevator contractors, the first being the current company servicing the elevator who had provided the bid to the seller. All three contractors visited the property to review the issues associated with the bid to repair the Sheave and conducted a general inspection of all three elevators. Results from each visit are displayed in the table below:
Contractor Opinions | Sheave Repair Bid Opinion | Other Inspection Findings |
---|---|---|
Contractor 1 (Existing Elevator Contractor Servicing the Building) |
Opinion: The Sheave looks worn and needs replaced (Bid Confirmed) Recommendation: Repair Sheave and Conduct 5 year load test. |
None |
Contractor 2 |
Opinion: The Sheave looks worn and needs replaced (Bid Confirmed) Recommendation: The rest of the equipment looks very old too. Should replace entire system. |
The commutator on elevator #1 (currently operating) is out of round and the brushes are sparking during operation. |
Contractor 3 |
Opinion: The Sheave looks OK, the emergency brakes look worn and could be the cause of the load test failure. Recommendation: Conduct a 5 year load test, observe the failure in action and run tests. |
The commutator on elevator #1 (currently operating) is out of round and the brushes are sparking during operation. |
Kouri Management began calling on DC Motor contractors around the nation to get an idea of the repair costs for the commutator issues on Elevator #1. Large DC Motor repair is a specialized field and there are limited options in the state. As calls were made, it became increasingly apparent that the motor would need to be removed from the building via crane and transported to one of the many motor shops called upon. This would not be an option until after purchase of the building because part of the roof would need to be removed to facilitate removal of the motor. KMC Properties LLC would not be willing to purchase the property until all 3 elevators were operational or had a repair plan with a fixed cost that was financially acceptable. After continued persistence a contractor in Texas was identified that was willing to attempt a field repair on the motor. The contractor flew in and conducted the repair on the commutator successfully and put Elevator #1 back operation. This repair cost $24,000 and represented a significant investment in the property prior to completing the purchase.
A week later, the 5 year load test was conducted, tests were performed and from measuring the electric current while going up vs down it was discovered that counter weight was undersized by 50%, increasing the effective load of the elevator significantly and causing it to fail the 5 year test. The counter weight was increased to specification at a minimal cost and the 5 year load test was ran once more, Elevator #2 passed, the results were submitted to the state and the elevator was put back in service. KMC Properties LLC was able to complete the purchase with 3 elevators in operation and good working order.
Experts and specialist contractors are as important as players to a football team but if they are not provided with direction and vision from the coach and organized into a “play” the team cannot compete at a high level. The coach must pass judgment on each player’s performance and select the right talent for the right situation. The table above clearly illustrates the variance in expert opinions on a situation that had few right answers. It is extremely important that property and asset managers possess the skills to pass judgment on the opinions of the experts while at the same time, putting in the effort to solicit enough expert opinions to paint a clear picture to judge upon. Many who participate in high level property and asset management choose to delegate the problem solving to the subject matter experts who are often 3rd party contractors. While this does create results, they are far short of the best possible outcomes.
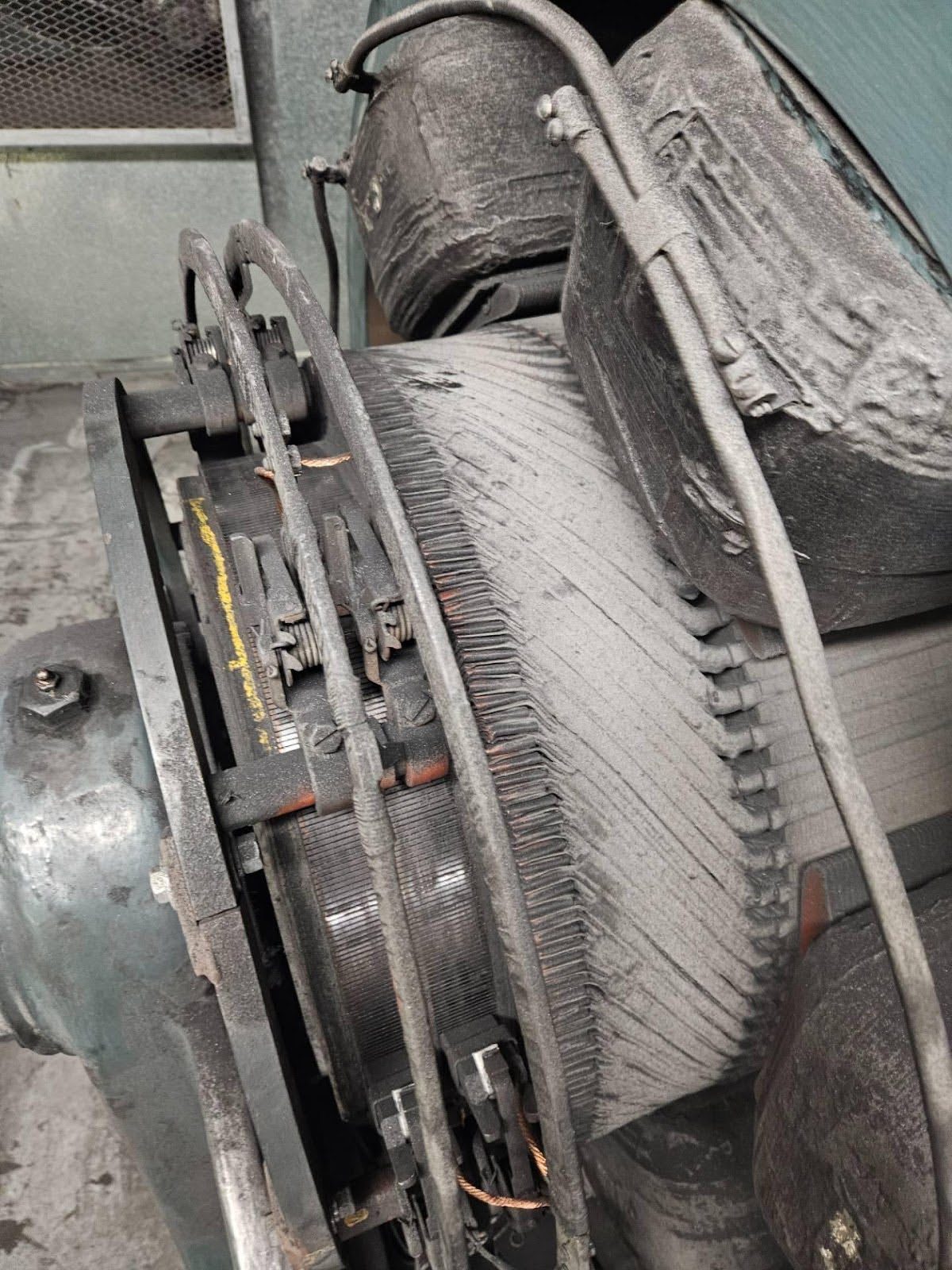
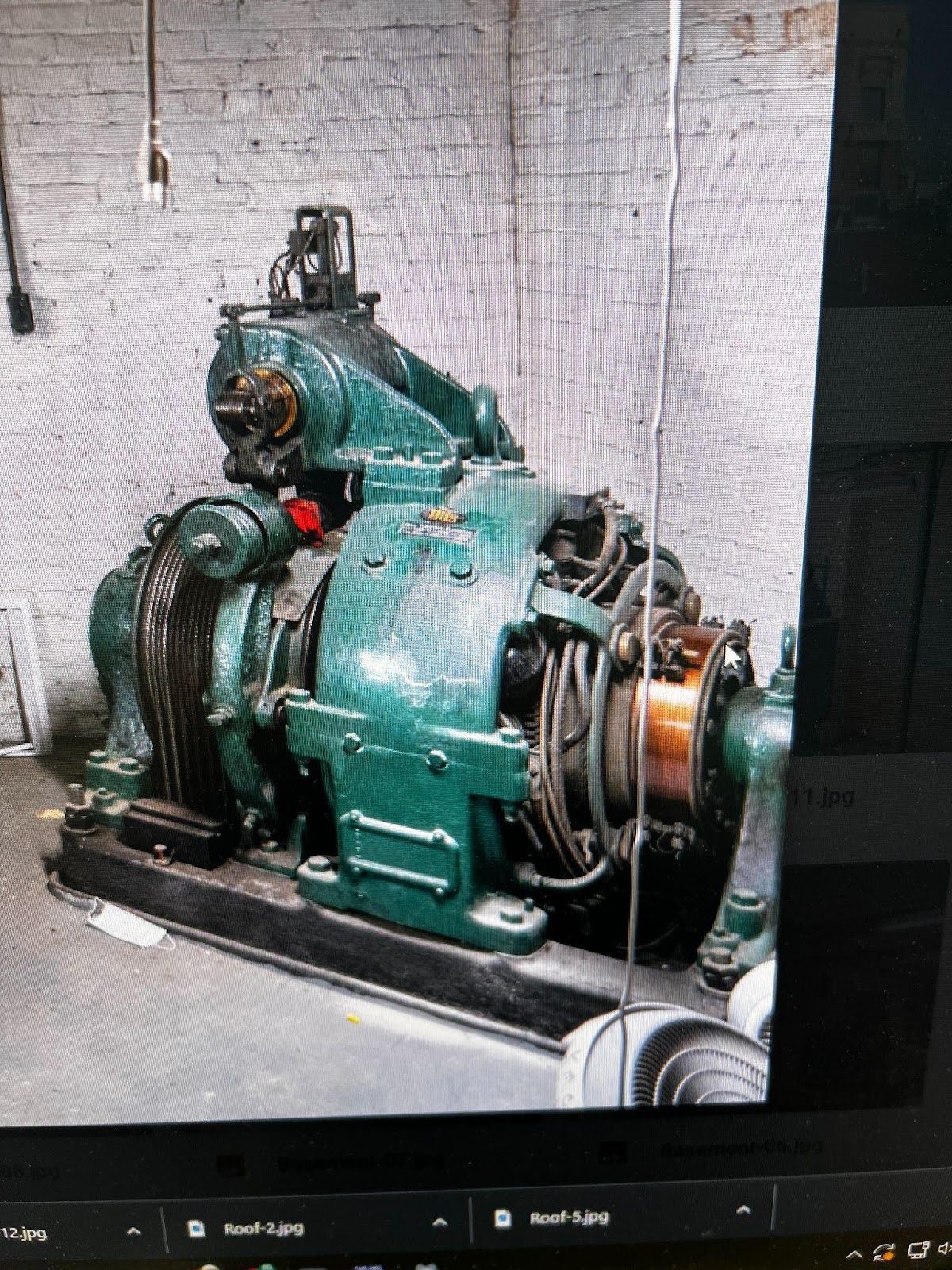
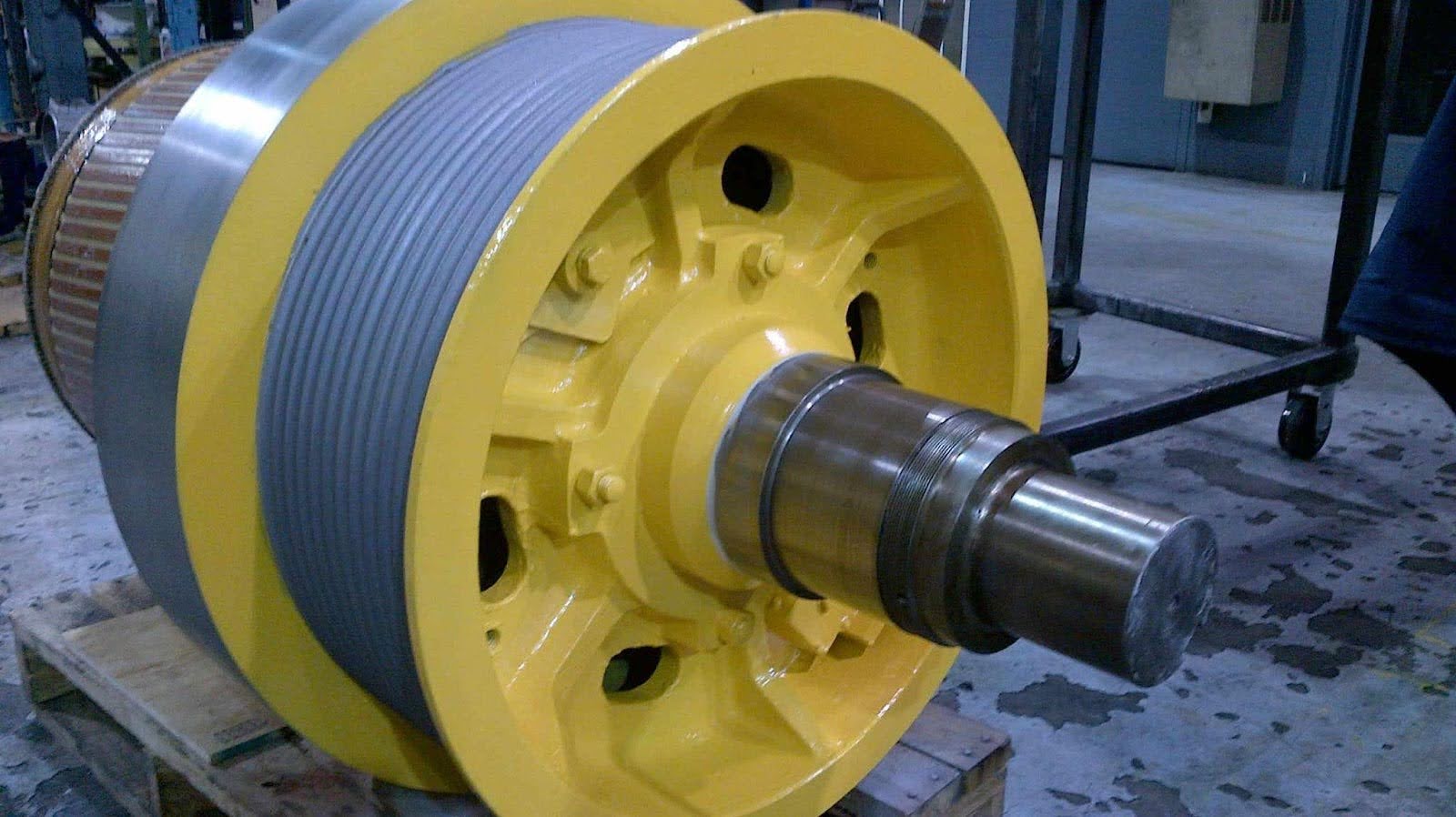
Part 3 – “Conditioned into complacency” Resolution of the Closed Loop HVAC System at Kensington Tower Apartments
Kouri Management was heading into the first summer after taking management on the Kensington Tower Apartments in the spring of 2021. The 12 story highrise property features a closed loop, water cooled heat pump system that provides HVAC to the property year round. A heat pump is kind of like an air conditioner that runs in reverse, a reversing valve can be actuated and the system can switch between heat and cooling. A window air conditioner effectively extracts heat from the air in the room and transfers that heat to the air outside. A water cooled air conditioner extracts heat from air in the room and transfers it to water that is flowing in a pipe, circulating through the building in the case of the Kensington Tower Apartments. This circulating water is referred to as the “Building Loop” As the collective heat from all the apartments in the building gets extracted by the Building Loop, the water heats up significantly. This heat must be extracted from the Building Loop or the temperature would continue to rise until the water boiled and damage occurred to the system. In the case of the Kensington Tower Apartments and like many other similar systems, the Building Loop passes through a plate and frame heat exchanger where it exchanges heat with another circulating water loop, called the “Cooling Tower Loop”. After the Cooling Tower Loop takes heat from the Building Loop, it flows to the Cooling Tower, which is another type of heat exchanger that uses evaporation to transfer heat from the water to the air outside. This system may sound over complicated when explained in paragraph format but it is a very effective HVAC solution for properties that do not have the following:
- Roof space to facilitate air cooled heat pumps or AC
- Allowance of Window or Wall ACs (Most Class A and B and Historic Properties demand a central HVAC solution)
- Gas service to all dwelling units
Many Historic High Rise Redeveloped Properties feature this type of system for the above reasons.
As management commenced through the Spring of 2021 and Kouri Management became acquainted with residents, stories started to surface about how the building has lost air conditioning capabilities every summer for the last 5 years when temperatures exceeded 90 degrees. The system had been maintaining sufficiently in the milder temperatures of April and May. A significant local mechanical contractor had serviced the building for the last 10 years. The contractor had replaced the Boiler and Cooling Tower the previous year. The contractor was consulted about the Resident stories and they assured that this summer would be different with the new equipment. In early June the building was put to the test and failed. Kouri Management received multiple calls from residents about their AC/heat pump units tripping out. The Building Loop Temperature was checked and the temperature was 130F. The AC/heat pump units require water at 100F and lower or they overheat and trip the breaker. The contractor was called to the property, after inspecting the equipment temperatures, their diagnosis was that the plate and frame heat exchanger that transfers heat from the Building Loop to the Cooling Tower Loop was clogged from microbial growth in the cooling tower and that a chemical clean of the heat exchanger would be required. The contractor charged around $3,000 for the chemical clean and warranted that it would resolve the issue. Kouri Management had noted in the sellers historic financials that the seller had paid for multiple chemical cleans of the heat exchanger in the previous year. Kouri Management asked the contractor if it would be more effective to disassemble the heat exchanger and clean it manually but the contractor stated that it would take a full week without AC and cost upwards of $20,000. The chemical clean was completed and all of the AC/heat pumps in the building were reset and turned on. By that time it was evening and the temperature outside had dropped, there was no confirmation that the chemical clean had resolved the issue. A week later the same problem occurred again despite the recent chemical clean.
The Solution
During the week between the two incidents Kouri Management had conducted research on the dynamics of the building system and called on other expert opinions about the problems that were occurring. It was a known fact that heat was not being transferred out of the Building Loop at a high enough rate to keep up with the collective heat generated from the resident AC/heat pump units. It was known that the heat lost by the building loop is equal to the water temperature entering the heat exchanger minus the exit temperature, multiplied by the mass (Flow Rate) of the water multiplied by the heat capacity of water. (Shown in the Equation 1 below)
Equation 1:
It was also known that the heat lost by the Building Loop would be equal to the Heat Gained by the Cooling Tower Loop and the heat gained by the Cooling Tower Loop would follow a similar equation (see equations 2 & 3 below)
Equation 2:
Equation 3:
Setting Equations 1 & 3 equal to each other, it is apparent that the “C” term cancels out and does not matter since in the case of the Building Loop and Cooling Tower Loop, the Fluid is water.
That contractor had stated that the heat exchanger was “clogged” by microbial growth from the cooling tower and they had prescribed a chemical clean to resolve the issues. A “clog” means a restriction or decrease in FLOWRATE which affects the equations above. Testing flow rate in a pipe is very hard and expensive and was not feasible in the situation. Temperature however, was easily measurable. The temperature was taken at the inlet and outlet of both the Building Loop and the Cooling Tower Loop at the heat exchanger.
When it was 85 Degrees outside the temperatures would typically read the following:
A difference of 20 Degrees in the Cooling Tower Loop and 2 Degrees in the Building Loop. From the equations above, this would indicate that the Building Loop FLOWRATE would be 10X the Cooling Tower Loop FLOWRATE. The pipes were the same size so this temperature situation seemed wrong to Kouri Management and all other parties consulted.
When the issue occurred a week after the first incident Kouri Management called the contractor back into the building. The contractor stated that the heat exchanger seemed to be clogged again and would need another chemical clean. The logical sequence above was explained to the contractor but he disputed: “it’s not that simple, there are so many moving parts, the real world is a lot different than your school book”. As someone who values real world experience over his own engineering degree, Alex Kouri, who was meeting with the contractor that day, shrugged his shoulders. The contractor continued to “represent that after a chemical clean of the heat exchanger, all debris would be removed and nothing could be left to cause a clog”. The contractor warranted the effectiveness of the first chemical clean so his team conducted a second clean of the system. This time the temperatures stayed hot throughout the evening and when the system was turned back on after the clean, it continued to overheat. The contractor threw up his hands and said they would have to come back another time and investigate further. That week the temperatures consistently remained above 90 degrees. The Kouri Management team had to leave the lobby of the building unconditioned and run heat in the vacant units to remove heat from the Building Loop in order to allow residents to have cooling in their dwellings. The contractor sent an invoice for the chemical clean and stated that they could not help anymore. Kouri Management continued the investigation and troubleshooting, another contractor that was called on advised checking the Flow Rate specifications in the mechanical system drawings for the building. The drawings were reviewed and stated that the Building Loop and the Cooling Tower Loop were designed to operate at an equal flow rate of 400 Gallons per minute. If the conservation of energy was correct, per the equations above, then if the Building Loop was operating at spec (400 GPM) the Cooling Tower Loop must be operating at 40 GPM 10% of specification. With this knowledge, it was almost certain that the Cooling Tower Loop was restricted. Kouri Management began calling on contractors for bids to disassemble the heat exchanger. After talking with several contractors it was determined that the in-house maintenance team was capable of disassembling the heat exchanger under the supervision of a licensed mechanical contractor. Materials necessary for the job were ordered and the heat exchanger was disassembled, cleaned and reassembled in the fall of 2021. Significant debris was discovered in the heat exchanger, much of it metals and calcium which would not have dissolved in a chemical clean. Since the cleanout of the heat exchanger, the building AC system has operated with excess capacity (as it was designed to) over the last 2 seasons even at outside temperatures well above 100F.
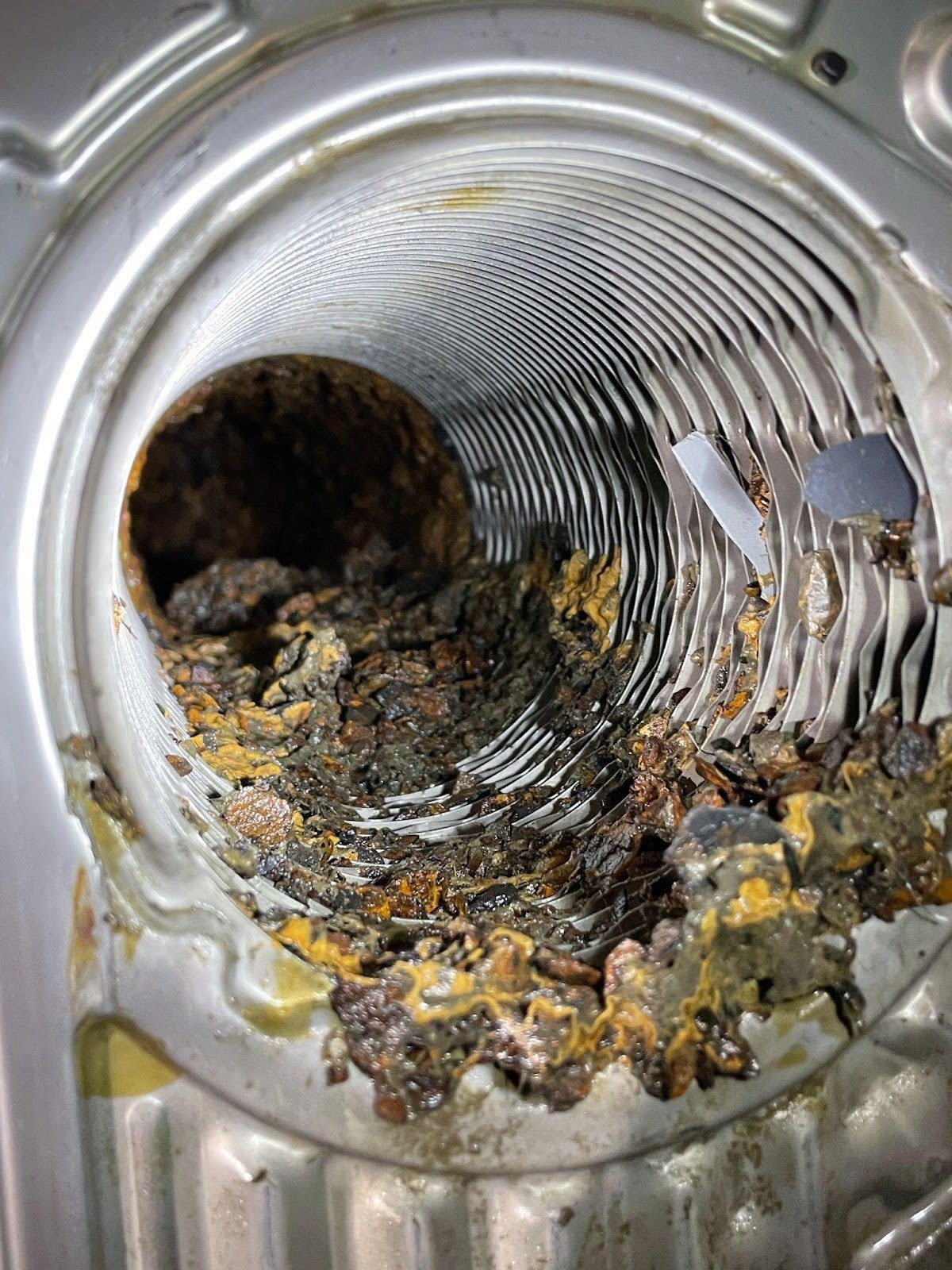
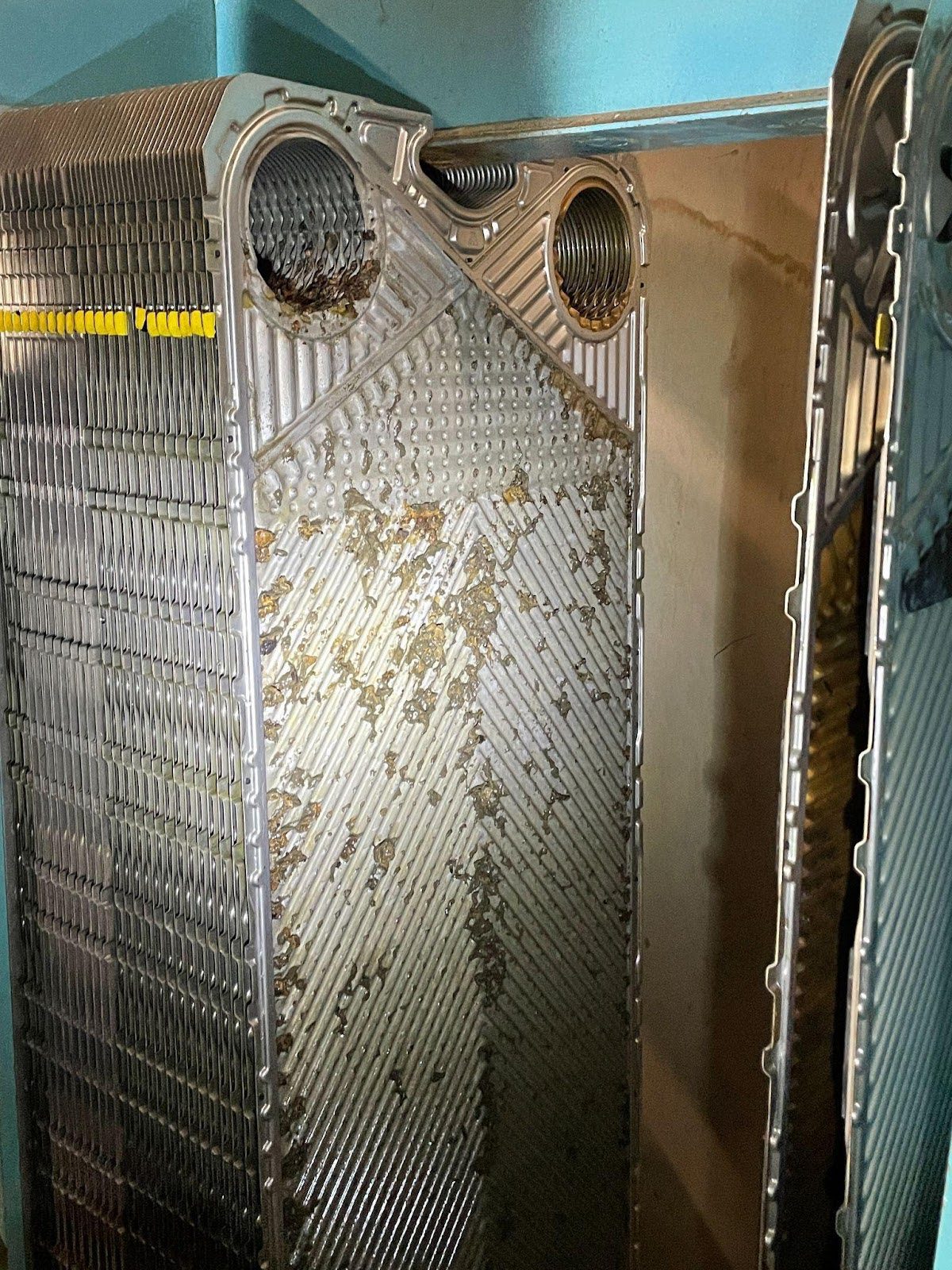

Kouri Management
604 Walnut St
Des Moines, IA 50309
Omaha Office
505 S 16th St
Omaha, NE 68102
Council Bluffs Office (Headquarters)
132 W Broadway
Council Bluffs, IA 51503